Learn more about combustible dust, exploring what it is, how it can lead to explosions, its classifications, real-world examples and most importantly prevention measures to keep your workplace safe.
What Is Combustible Dust?
Combustible dust refers to fine particles or dust that can catch fire and explode when they are suspended in the air and come into contact with an ignition source. These dust particles are typically produced from various materials such as metals, chemicals, plastics, wood, agricultural products or even food substances.
Combustible Dust Explosion
A combustible dust explosion is a violent and potentially deadly event that occurs when certain conditions are met. There are five key elements that must be present for a combustible dust explosion to occur. These elements are often referred to as the “Dust Explosion Pentagon” or “Five Elements of Dust Explosion”. They are:
Five Elements Of Dust Explosion
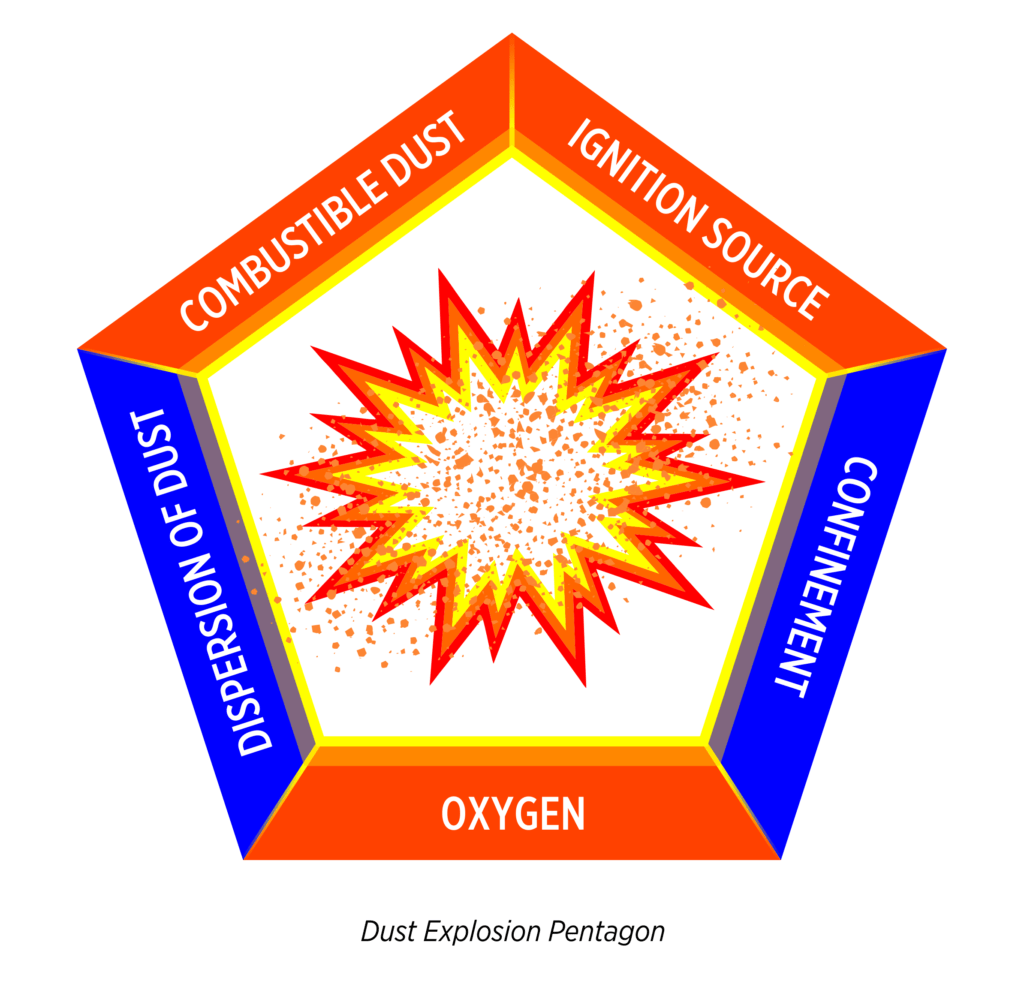
Combustible Dust: The presence of fine combustible dust particles in the air is the first element. These dust particles can come from various sources such as wood, metal, plastic, food, chemicals or other materials. The dust must be finely divided creating a dust cloud or layer.
Oxygen: Oxygen is essential for combustion. Dust explosions occur when there is an adequate supply of oxygen in the air. For an explosion to take place the oxygen concentration needs to be above a certain threshold which is typically around 13% to 15% by volume.
Ignition Source: An ignition source is required to initiate the combustion of the combustible dust and air mixture. Common ignition sources include sparks, open flames, hot surfaces, electrical equipment, friction and electrostatic discharges.
Dispersion of Dust: The dust must be dispersed into the air to form a dust cloud. This can occur naturally through processes like mixing, conveying or dust settling in the air. A finely dispersed dust cloud is more prone to explosion than a settled layer of dust.
Confinement: The dust cloud needs to be confined within an enclosed or semi-enclosed space. The confinement increases pressure and allows for the build-up of explosive concentrations of dust and oxygen. This is a critical factor in the severity of the explosion.
When all these elements come together and the conditions are just right a combustible dust explosion can occur. These explosions can lead to significant damage, injuries and even loss of life. To prevent dust explosions, it’s crucial to implement safety measures and practices in industries where combustible dust is present. Such as using proper ventilation, dust control and the elimination of potential ignition sources.
Combustible Dust Classifications
Combustible dust classification is a system used to categorize and assess the flammability and explosion hazards of various types of dust particles. This classification helps industries and regulatory bodies manage safety and implement appropriate measures to prevent dust explosions. The classification typically involves dividing combustible dust into different classes and divisions, based on specific characteristics. Here is a general overview of combustible dust classification:
Class: Combustible dust is classified into one of three primary classes based on the material’s properties.
- Class I – Dusts that are easily ignitable and present a significant explosion hazard. These are typically organic materials like wood, paper and certain metals.
- Class II – Dusts that are electrically conductive and may be ignitable. This class includes metal dust, carbonaceous dust and more.
- Class III – Dusts that are not easily ignitable but can become explosive if suspended in the air in sufficient quantities. These include agricultural and plastic dust.
Division: Within each class, there are further divisions to classify the level of hazard and the likelihood of ignition.
- Division 1: Dust is present continuously, frequently or intermittently under normal operating conditions and can create an explosion hazard.
- Division 2: Dust is present only under abnormal conditions such as equipment breakdown or malfunction.
Group: The material’s group designation is based on its ignition sensitivity and explosibility. There are different group designations for Class II and Class III dusts.
Group E – Dusts that are electrically conductive and include conductive metal dust such as aluminum, magnesium and others.
Group F – Dusts that are carbonaceous like coal, carbon black, charcoal and plastic.
Group G – Dusts that are neither electrically conductive nor carbonaceous, which includes a wide range of organic and non-metallic materials.
The classification of a particular type of dust depends on its unique properties and characteristics. Employers and safety professionals must perform dust hazard assessments to determine its classification. It’s important to note that different industries and regions might have their own specific criteria and standards for classifying combustible dust. Understanding the classification of the dust in your particular workplace is essential for implementing appropriate safety measures and controls.
Combustible Dust Examples
Many different substances can form combustible dust and here are some examples of materials that can create combustible dust hazards:
Wood dust: Fine particles generated from woodworking activities such as sanding and sawing can become combustible when suspended in the air.
Metal dust: Certain metals like aluminum, magnesium, and titanium can form combustible dust when they are finely ground or generated during metalworking processes.
Coal dust: Dust generated from coal mining, handling and processing can be highly combustible.
Grain dust: Grains like wheat, corn, and rice produce dust during handling, storage and milling, which can become combustible.
Sugar dust: Sugar processing can create fine sugar dust particles that are flammable when dispersed in the air.
Plastic dust: Fine particles from plastic materials like PVC and nylon can pose a combustible dust hazard, particularly in industrial settings.
Rubber dust: Dust generated from rubber processing can also become combustible when suspended in the air.
Textile fibers and dust: Materials like cotton and rayon produce dust during manufacturing processes that can be a fire risk.
Pharmaceutical dust: Fine particles generated during the production of pharmaceuticals can be combustible and pose safety risks.
Dyes and pigments: Dust from various coloring agents used in industries can be a source of combustible dust.
Paper and pulp dust: Paper mills and pulp production can generate dust that, when airborne, can lead to explosive situations.
Charcoal: Charcoal dust can be combustible and dangerous when not properly managed.
Organic dust: This category includes dust from organic materials like sawdust and coffee grounds, which can be combustible.
Cocoa powder: Cocoa processing generates fine cocoa powder, which can pose a combustible dust hazard.
Starch dust: Dust from starch materials can become combustible when suspended in the air.
Sulfur dust: Sulfur in powder form can be a source of combustible dust.
Pesticides and herbicides: Some agricultural chemicals, when in dust form, can present a fire risk.
Chemical dust: Dust from various chemicals, including pharmaceuticals and talc, can be combustible.
Coal tar pitch dust: This byproduct of coal processing can be combustible in dust form.
Fertilizer dust: Dust generated from handling and processing fertilizers can be combustible.
Metalworking dust: Dust from metalworking processes like grinding and polishing can be a hazard, especially with certain metals.
Flammable liquids as aerosols or mists: Liquid particles in the air can be flammable and pose a risk.
Explosive powders: Certain explosive materials can become a hazard when in powdered form and dispersed in the air.
Magnesium alloys: Dust generated from magnesium alloys can be highly combustible.
Carbon black: This fine powder produced in the production of rubber and other materials is highly combustible when airborne.
Please note that the list above is not exhaustive and not all of the materials listed are equally explosive. The Kst value compares the relative explosion severity of a dust to other dusts. A Kst value is a single digit and the greater the digit the more explosive the dust. The chart below depicts dust explosion classes based on Kst ranges as well as common flammable dust compounds that fall within those classes.
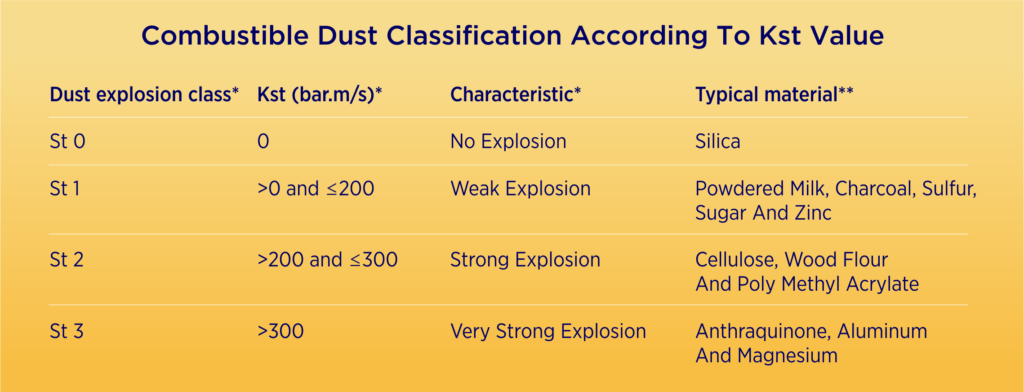
* OSHA CPL 03-00-008 – Combustible Dust National Emphasis Program.
** NFPA 68, Standard on Explosion Prevention by Deflagration Venting.
What Is Kst Value?
The “Kst value” typically refers to the deflagration index in the context of industrial safety and explosion protection. It is a measure used to assess the explosiveness of a dust or gas mixture.
Kst is an abbreviation for “deflagration constant.” It quantifies the rate at which a dust or gas mixture can undergo a deflagration, which is a fast combustion process that results in the release of energy and pressure. The Kst value is used to classify dust or gas mixtures according to their explosiveness and potential for causing explosions. A higher Kst value indicates a more explosive mixture. Understanding the Kst value is important in industries where dust or gases are present, such as in manufacturing, chemical processing or agriculture. Proper handling, storage and safety measures are necessary to mitigate the risks associated with materials that have high Kst values.
However, it’s important to note that even with a low Kst value, safety precautions and mitigation measures should still be in place to prevent any potential incidents and ensure a safe working environment.
Prevention of Combustible Dust Hazards
Preventing combustible dust incidents is crucial for workplace safety. Combustible dust can lead to explosions and fires if not managed properly. Here are some key measures to prevent combustible dust hazards:
Dust Hazard Analysis (DHA): Conduct a thorough assessment to identify and evaluate potential dust hazards in your workplace. This should include the type of dust, its explosibility characteristics and where it accumulates.
Housekeeping: Maintain a clean and organized workspace. Regularly clean up dust accumulations, both inside and outside of equipment to minimize the risk of ignition.
Dust Collection and Ventilation: Install dust collection systems with proper ventilation to capture and contain combustible dust. Make sure these systems are regularly maintained and kept in good working condition.
Explosion Protection: Implement explosion protection measures where necessary. This can include explosion vents, isolation systems or suppression systems to mitigate the potential damage of an explosion.
Electrical Equipment: Use dust-resistant or dust-tight electrical enclosures and wiring. Regularly inspect and maintain electrical systems to prevent sparks that could ignite dust.
Static Electricity Control: Implement static control measures such as grounding and bonding in areas where combustible dust is present to prevent static discharge.
Workplace Design: Ensure the design of the workspace minimizes dust accumulation and dispersion. This may involve using dust-free materials or coatings on surfaces.
Training: Educate employees about the hazards of combustible dust and train them on safe handling and clean-up procedures.
Hot Work Permit: Implement a hot work permit system for activities like welding and cutting, ensuring that potential ignition sources are controlled during such operations.
Safety Standards: Comply with relevant safety standards and regulations that pertain to your industry and location. Ensure your facility meets or exceeds these standards.
Emergency Response: Develop and communicate emergency response plans to deal with potential dust-related incidents including fire suppression and evacuation procedures.
Material Handling: Use equipment and processes that minimize dust generation during material handling and processing.
Regular Inspections: Conduct routine inspections of equipment, systems and processes to identify and address potential issues before they become hazards.
Risk Assessment: Continuously assess the risk associated with combustible dust in your facility and update safety measures as needed.
Documentation: Maintain detailed records of dust hazard assessments, safety measures, training and incidents. These records can help in identifying areas for improvement.
Preventing combustible dust incidents requires a proactive approach, ongoing training and a commitment to maintaining safe working conditions. Regular safety audits and employee involvement in hazard identification are also essential in creating a safer workplace.
Conclusion
Understanding combustible dust is not just a matter of compliance with regulations; it’s a critical step in safeguarding the well-being of workers and the integrity of industries where dust is prevalent. By being aware of the risks, adhering to safety measures and encouraging a culture of safety, we can significantly reduce the potential for combustible dust incidents.
FAQs
What is the main risk associated with combustible dust?
The primary risk is the potential for explosive ignition when dust is present in sufficient concentrations.
Which industries are most susceptible to combustible dust hazards?
Industries such as manufacturing, food processing, pharmaceuticals, agriculture and woodworking are at higher risk.
What is Dust Hazard Analysis (DHA)?
DHA is a process that identifies potential sources of combustible dust and assesses the associated risks.
How can employees contribute to preventing combustible dust incidents?
Employees play a crucial role by following safety protocols, participating in training and maintaining good housekeeping practices.
What are some common explosion protection systems for combustible dust?
Explosion venting and suppression systems are commonly used to mitigate the effects of a dust explosion.
Also Read
Cleaning Solar Panels For Maximum Efficiency
Industrial Dust: Understanding its Impact and Management
9 thoughts on “Combustible Dust: Understanding Explosion, Classification And Prevention”